Welcome! I suppose I should explain what this site is for and why its here. If you are like me and enjoy the old wind-up vintage watch and you dont want to make super accurate time-keeping a part of your life then maybe we share something in common. If you also enjoy listening to Pink Floyd, walking dogs and travel then we probably share even more in common.
…its like owning a small scale classic car:
Its not about knowing what time it is. Nobody is ever going to come up to you and admire the clock on your phone. Its about creating a piece of work and in some cases a piece of art thats unique. Its about owning a small piece of history and carrying it with you on your wrist. All you need is time, patience and a little creativeness.
The site will show you how to make a vintage watch for yourself. It follows the theme of the Italian Vintage Panerai divers watches from the 1940’s to the 1950’s. People usually start by buying a movement from places like EBay and then buying a watch case which they shape, polish and build into a finished watch. Nothing on this site is modern or available in the high street.
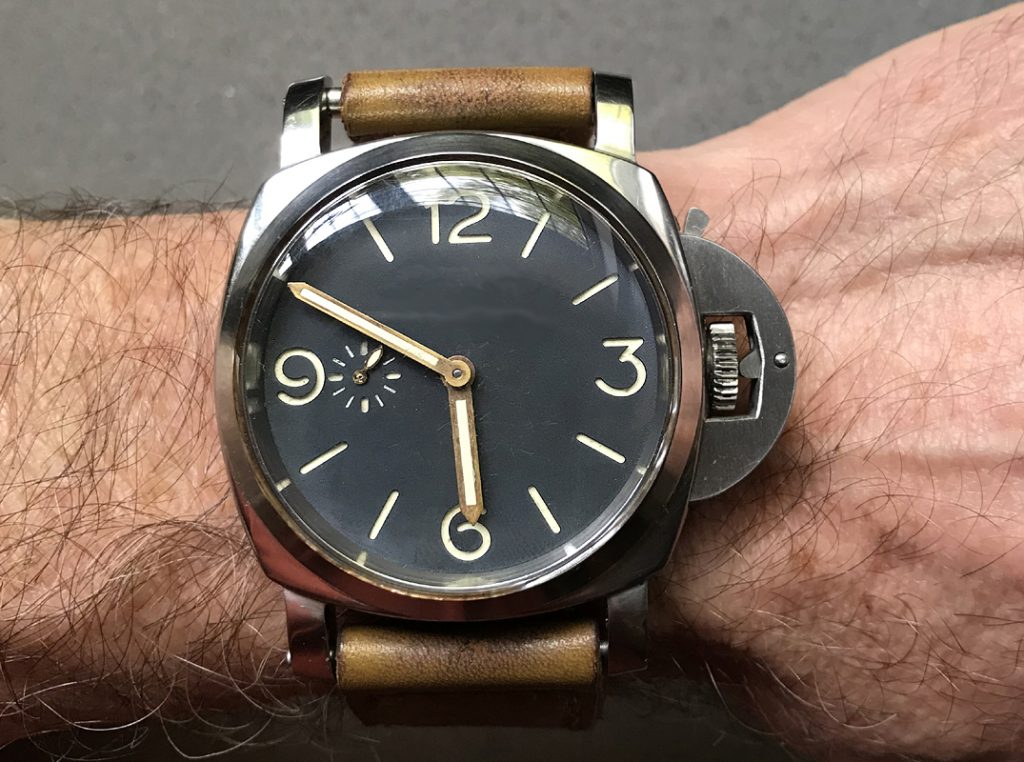